1G to 6G In The Welding Industry: Weld Position Division And Welding Techniques
Release Time:2024-06-11
1G to 6G In The Welding Industry: Weld Position Division And Welding Techniques
The progression from 1G to 6G in welding involves different weld positions and techniques, each presenting unique challenges and requiring specific skills. Here’s a detailed look at each weld position and the associated techniques:
1G Position (Flat Position)
- 1. Description: The pipe or plate is positioned horizontally, and the weld is performed from the top.
- 2. Techniques:
- 1) Electrode Angle: Hold the electrode at a slight angle (10-15 degrees) to direct the weld pool.
- 2) Travel Speed: Maintain a consistent speed to ensure uniform bead appearance.
- 3) Heat Control: Adjust the amperage to avoid excessive heat which can lead to burn-through.
2G Position (Horizontal Position)
- 1. Description: The pipe is positioned vertically, and the weld is performed horizontally.
- 2. Techniques:
- 1) Electrode Manipulation: Use a side-to-side weaving motion to fill the joint.
- 2) Gravity Compensation: Counteract gravity to prevent the weld pool from sagging by adjusting the electrode angle.
- 3) Heat Management: Adjust the amperage to prevent overheating the weld pool.
3G Position (Vertical Position)
- 1. Description: The weld is performed vertically, either uphill (bottom to top) or downhill (top to bottom).
- 2. Techniques:
- 1) Vertical Uphill Welding: Use a zig-zag or circular motion to control the weld pool and achieve good penetration.
- 2) Vertical Downhill Welding: Use a faster travel speed to prevent excessive penetration and maintain a clean bead.
- 3) Heat Control: Lower the amperage for vertical uphill to avoid excessive heat buildup.
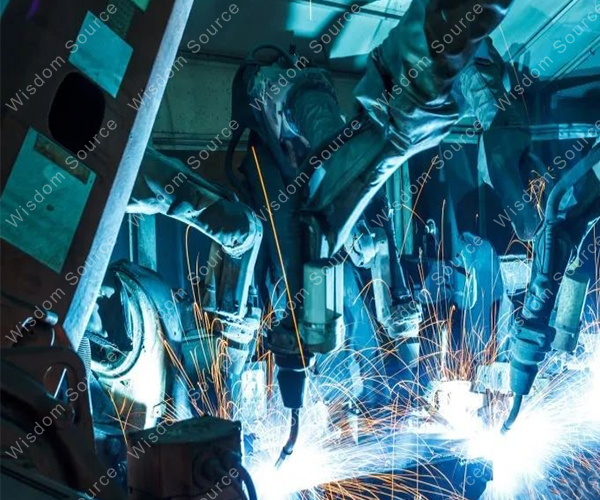
4G Position (Overhead Position)
- 1. Description: The pipe or plate is positioned horizontally, and the weld is performed from underneath.
- 2. Techniques:
- 1) Weld Pool Control: Use short, controlled welds to prevent dripping and maintain a stable weld pool.
- 2) Body Positioning: Maintain a comfortable stance to reduce fatigue and ensure steady hand movements.
- 3) Heat Management: Lower the amperage to avoid excessive heat, which can lead to drips and sagging.
5G Position (Pipe Fixed Horizontal)
- 1. Description: The pipe is positioned horizontally but remains fixed; the welder must move around the pipe to complete the weld.
- 2. Techniques:
- 1) Combination Techniques: Employ techniques from flat, horizontal, vertical, and overhead positions.
- 2) Consistent Movement: Move smoothly around the pipe, maintaining a consistent bead profile.
- 3) Heat Control: Adjust settings based on the changing orientation of the weld.
6G Position (Pipe Fixed at 45 Degrees)
- 1. Description: The pipe is fixed at a 45-degree angle, and the welder must weld in all positions (overhead, vertical, horizontal).
- 2. Techniques:
- 1) All-Position Mastery: Combine techniques from all previous positions.
- 2) Steady Hand and Coordination: Maintain steady movements and precise control over the electrode.
- 3) Heat Management: Continuously adjust amperage and travel speed to accommodate the changing weld pool dynamics.
Welding Techniques for Each Position
1. Electrode Manipulation
- 1) Weaving: Moving the electrode side to side to create a wider bead and fill gaps.
- 2) Stringer Beads: Using straight, narrow beads for better control and penetration.
2. Travel Speed and Angle
- 1) Consistent Speed: Maintaining a steady speed to ensure even heat distribution and bead appearance.
- 2) Optimal Angle: Adjusting the electrode angle to direct the weld pool and control penetration.
3. Heat Control
- 1) Amperage Adjustment: Modifying the current settings to suit the thickness of the material and position.
- 2) Preheat and Interpass Temperature: Preheating the material and controlling the temperature between passes to avoid defects.
4. Joint Preparation
- 1) Cleaning and Fit-Up: Ensuring the surfaces are clean and properly aligned to avoid defects.
- 2) Tack Welding: Using small welds to hold parts in place before final welding.
Summary
Progressing from 1G to 6G weld positions requires increasingly advanced welding techniques and skills. Each position challenges the welder to control the weld pool, manage heat input, and maintain consistent bead quality under different orientations. Mastery of these positions is essential for producing high-quality welds in various industrial applications, such as pipelines, structural fabrication, and aerospace.